What is Porosity in Welding: Recognizing Its Reasons and Enhancing Your Skills
What is Porosity in Welding: Recognizing Its Reasons and Enhancing Your Skills
Blog Article
The Science Behind Porosity: A Comprehensive Guide for Welders and Fabricators
Comprehending the intricate systems behind porosity in welding is vital for welders and fabricators striving for flawless craftsmanship. From the structure of the base materials to the ins and outs of the welding process itself, a plethora of variables conspire to either exacerbate or relieve the visibility of porosity.
Understanding Porosity in Welding
FIRST SENTENCE:
Examination of porosity in welding exposes essential understandings right into the stability and top quality of the weld joint. Porosity, characterized by the presence of tooth cavities or gaps within the weld metal, is a typical worry in welding procedures. These gaps, otherwise appropriately resolved, can endanger the architectural integrity and mechanical homes of the weld, causing possible failures in the finished product.
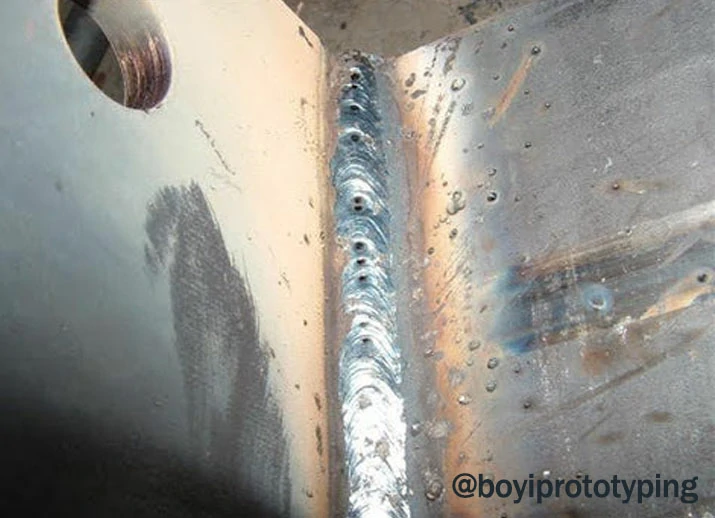
To discover and measure porosity, non-destructive testing methods such as ultrasonic testing or X-ray assessment are usually used. These strategies enable the identification of internal problems without jeopardizing the integrity of the weld. By evaluating the size, shape, and distribution of porosity within a weld, welders can make informed choices to enhance their welding processes and achieve sounder weld joints.
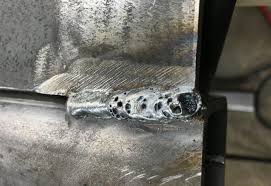
Aspects Affecting Porosity Development
The occurrence of porosity in welding is influenced by a myriad of elements, varying from gas protecting effectiveness to the ins and outs of welding parameter settings. Welding specifications, including voltage, existing, travel rate, and electrode type, additionally effect porosity development. The welding method employed, such as gas metal arc welding (GMAW) or protected steel arc welding (SMAW), can influence porosity formation due to variants in warm circulation and gas protection - What is Porosity.
Results of Porosity on Weld Quality
Porosity formation significantly jeopardizes the architectural honesty and mechanical residential properties of welded joints. When porosity exists in a weld, it creates spaces or dental caries within the material, minimizing the general stamina of the joint. These gaps act as tension focus factors, making the weld a lot more susceptible to cracking and failure under lots. The existence of porosity additionally damages the weld's resistance to rust, as the caught air or gases within the gaps can respond with the surrounding setting, leading to degradation over time. Additionally, porosity can hinder the weld's ability to endure stress or effect, additional endangering the total top quality and integrity of the welded structure. In vital applications such as aerospace, automotive, or structural building and constructions, where security and longevity are paramount, the damaging impacts of porosity on weld high quality can have severe effects, highlighting the importance of decreasing porosity via correct welding methods and procedures.
Strategies to Minimize Porosity
To boost the top quality of welded joints and make sure structural integrity, welders and producers use details techniques focused on reducing the formation of voids and dental caries within the material throughout the welding procedure. One efficient approach to reduce porosity is to make certain proper product preparation. This consists of thorough cleaning of the base steel to remove any type of contaminants such as oil, oil, or dampness that can add to porosity development. Furthermore, utilizing the proper welding criteria, such as the appropriate voltage, existing, and travel speed, is important in stopping porosity. Preserving a regular arc size and angle throughout welding likewise helps in reducing the likelihood of porosity.

In addition, picking the ideal securing gas and preserving appropriate resource gas circulation prices are essential in minimizing porosity. Using the appropriate welding strategy, such as back-stepping or using a weaving activity, can also help disperse warmth uniformly and decrease the possibilities of porosity formation. Finally, making sure appropriate air flow in the welding environment to get rid of any possible resources of contamination is crucial for accomplishing porosity-free welds. By implementing these methods, welders can efficiently minimize porosity and generate top notch bonded joints.
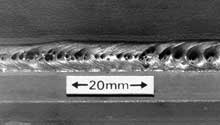
Advanced Solutions for Porosity Control
Executing sophisticated technologies and innovative techniques plays a crucial role in accomplishing premium control over porosity in welding this page procedures. Additionally, utilizing innovative welding techniques such as pulsed MIG welding or customized ambience welding can also assist mitigate porosity concerns.
One more innovative service includes the usage of innovative welding equipment. For example, utilizing equipment with built-in functions like waveform control and innovative source of power can enhance weld quality and decrease porosity dangers. The execution of automated welding systems with specific control click over here over specifications can substantially lessen porosity flaws.
In addition, including innovative surveillance and assessment technologies such as real-time X-ray imaging or automated ultrasonic screening can help in discovering porosity early in the welding process, permitting immediate rehabilitative activities. Generally, incorporating these innovative remedies can substantially boost porosity control and improve the overall quality of welded elements.
Conclusion
In conclusion, comprehending the scientific research behind porosity in welding is important for welders and makers to produce high-grade welds - What is Porosity. Advanced options for porosity control can further boost the welding process and make sure a solid and dependable weld.
Report this page